To maintain the livelihood of a company, it is ideal to reduce expenses wherever possible. Manufacturing losses provide an excellent start for industries to focus on. It is often difficult to find solutions to reducing manufacturing losses without removing essential procedures or labourers (robots & humans). Thankfully, with Production Monitoring, reducing manufacturing costs is an easier task.
How To Recover Using Production Monitoring
Manufacturers use production monitoring to obtain a complete view of a factory’s functions, in real-time. By collecting data from different areas of a production setting and displaying it in a global view, production monitoring provides employees with analytics and relevant information to increase efficiency and reduce costs. This is usually completed by installing sensors on essential equipment and linking it to a database to allow for centralized data. Manufacturing losses can quickly be reduced using this technology. The following are four of the most common losses which can easily be reduced with production monitoring.
Note: The injection molding industry is used as an example for a numerical comparison, but these are 4 important losses in any industry and the way to recover them is the same regardless.
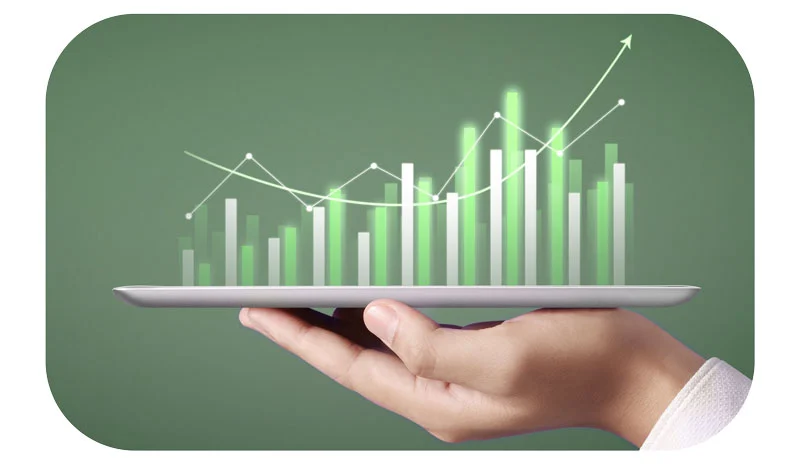
Downtime
Downtime refers to the time in which a machine or production floor is shut down due to maintenance or errors. Hence, downtime is one of the costliest losses in manufacturing. Unplanned downtime can be even more severe. Companies are often unprepared for unplanned downtime, and when it occurs, the reaction time causes a loss of productivity and money. Unplanned downtime is estimated to be 15 times more costly than planned downtime. In addition, according to an IBM study, 35% of manufacturers experience downtime at least once a month. If we take the injection molding industry as an example, a machine that stops for five minutes a day, every day, could result in a cost of a minimum of $150 a month. These avoidable monthly costs would eat up cash over time which could be used elsewhere.
Installing production monitoring allows for downtime to be easily avoided or reduced. Monitoring in real-time gives much-needed insight into your equipment by displaying whatever attributes would cause a crucial error (temperature, rate of production, etc.) and notifying workers if a problem would occur and where it would be. Depending on the production monitoring technology, planned downtime can even be automated to occur at an optimal time during production. Each of these benefits reduces the timespan during shutdowns and therefore helps minimize losses.
Cycle Times
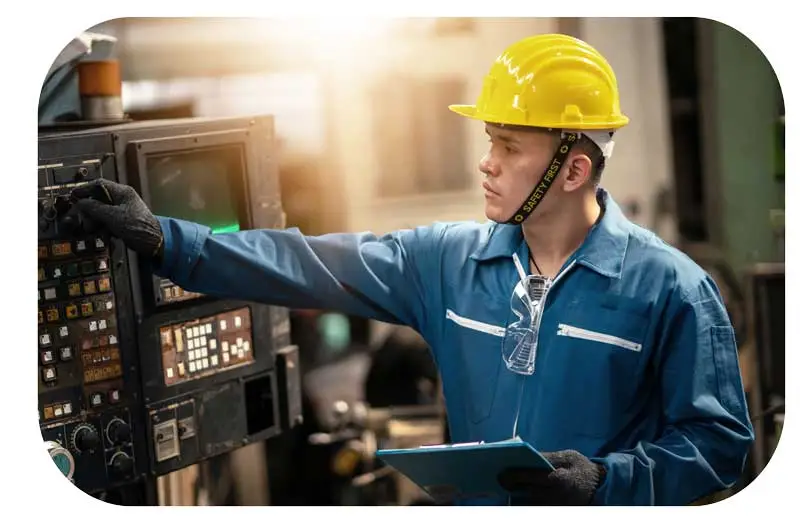
The amount of time in which a piece of equipment takes to work on an item is referred to as the cycle time. This is the main contributor to how quickly products are manufactured. Industries would ideally want to reduce cycle time to produce more products in the same timespan. To produce a work order on time, the machine must be within its cycle time. A delay of even one second means losses. For example, a molding machine that is 1 second out of its cycle for 1 day a week would cost a company $265 a month.
Production Monitoring can help locate areas in which cycle time could be improved. This technology can make automated adjustments to maintain consistent cycle times. This results in increased efficiency which could raise profits.
Rejects
Rejects are classified as products that don’t meet standards due to mistakes or errors during the manufacturing process. Depending on the complexity of the product, it may even be impossible to recycle it back into raw materials. Not to mention, if the manufacturing error is not corrected quickly, it may mass-produce rejected products, greatly affecting expenses. Rejects are unsellable, they waste raw materials, and decrease the yield of production. In the case of a molding machine, if it was to produce 10 incorrect parts every day, it could represent a loss of $140 a month, just in machine time.
Production Monitoring can easily solve this problem by noticing inconsistencies with the products or the production process. Like the downtime solution, Production Monitoring gives insight to equipment by sending notifications to a worker if a problem is occurring. Corrective action can then be taken to minimize the reject count. This in turn will maintain efficiency, and therefore sustain steady profits.
Data Collection & Reports
During a manufacturing timespan, it is important to gather data from your production floor to create performance reports. These reports are essential to increase overall efficiency. A worker could analyze the data and make corrections or improvements to the manufacturing process and increase profits. If a worker was to perform this by hand, it may be a lengthy process. For example, a worker who collects data from a molding machine 12 minutes a day, on a $25/hour pay would result in a cost of $120 a month.
By automating all data collection and reporting with production monitoring, it eliminates the need to perform it by hand and allows for data centralization and instant performance reports. This saves wage expenses and allows workers to focus on more meaningful tasks during the workday.
In conclusion, production monitoring is an essential process for any manufacturing environment. In the examples used above, a molding machine was subject to various errors which could be corrected using production monitoring. With each monthly cost combined, the company that owns the machine can save approximately $675 a month by installing this monitoring technology. Downtime can successfully be avoided, cycle times would be optimized, rejects reduced, and automated data reports would be collected. Each of these benefits allows for consistent savings from your manufacturing costs.