In today’s manufacturing climate, any company would ideally strive for better, faster, and cheaper ways to produce their goods. Doing so gives them an advantage over their competitors and therefore makes them a more desirable choice for consumers. The key is to reduce manufacturing time and cost while still ensuring all production requirements are met and problems are successfully avoided. Through the use of production line monitoring, both constraints can successfully be met. This would allow companies to save time and money and therefore give that necessary advantage.
What is Production Monitoring?
Production Monitoring is the process of taking data from a production line and displaying it in real-time. In other words, it collects information from different areas of a production line and displays all relevant data for an employee to review. This data can be analyzed to make efficiency improvements or simply to ensure no errors are currently affecting the machines.
Here are a few advantages of applying production monitoring:
Reduced Labor Costs
Before automated data acquisition was invented, production and operation data were collected manually. This means a machine operator or project engineer would be required to collect this data by observing each machine individually, calculating its efficiency, and analyzing the data at the recorded period of time. This method is quite inefficient when calculating overall equipment effectiveness, and consumes valuable time which workers are paid for when they could be used to perform other essential tasks.
Using production line monitoring, a company could reduce these labour costs by eliminating the need to check machines in person. Instead, important data could be collected in a matter of minutes, rather than a couple of hours manually. This would allow for a more accurate data collection (since the data would be recorded at the same time, rather than hours apart), and save valuable time which a worker could instead use to analyze the data.
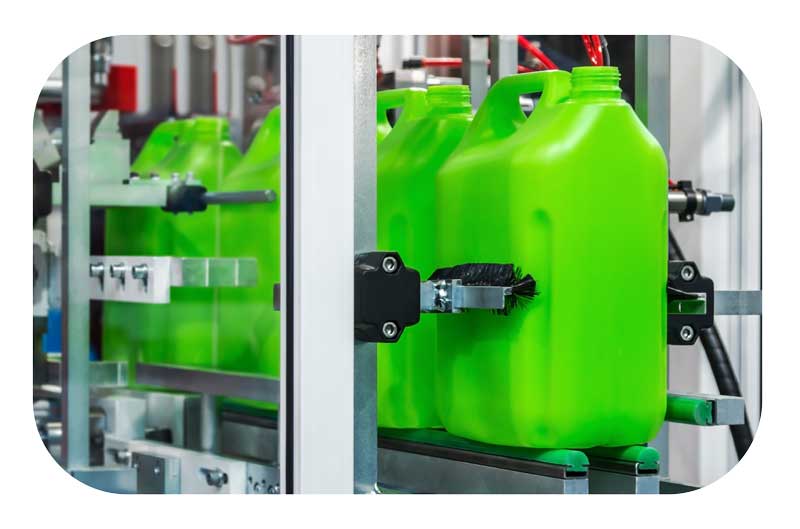
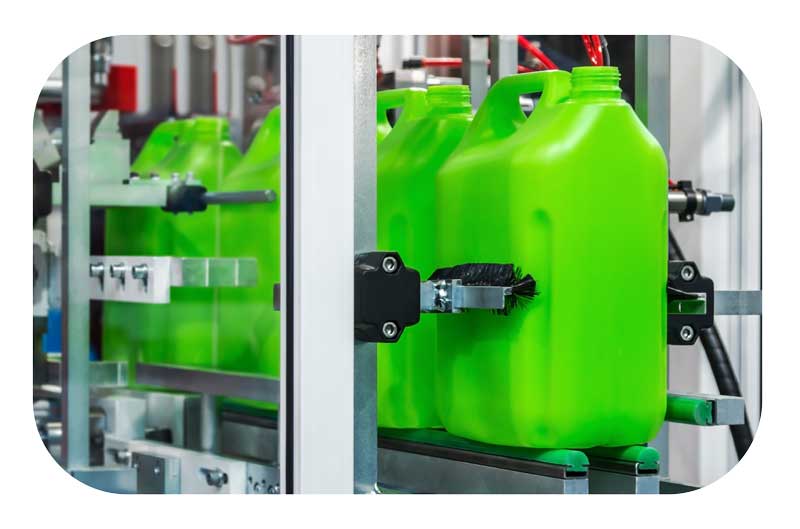
Reduced Labor Costs
Before automated data acquisition was invented, production and operation data were collected manually. This means a machine operator or project engineer would be required to collect this data by observing each machine individually, calculating its efficiency, and analyzing the data at the recorded period of time. This method is quite inefficient when calculating overall equipment effectiveness, and consumes valuable time which workers are paid for when they could be used to perform other essential tasks.
Using production line monitoring, a company could reduce these labour costs by eliminating the need to check machines in person. Instead, important data could be collected in a matter of minutes, rather than a couple of hours manually. This would allow for a more accurate data collection (since the data would be recorded at the same time, rather than hours apart), and save valuable time which a worker could instead use to analyze the data.
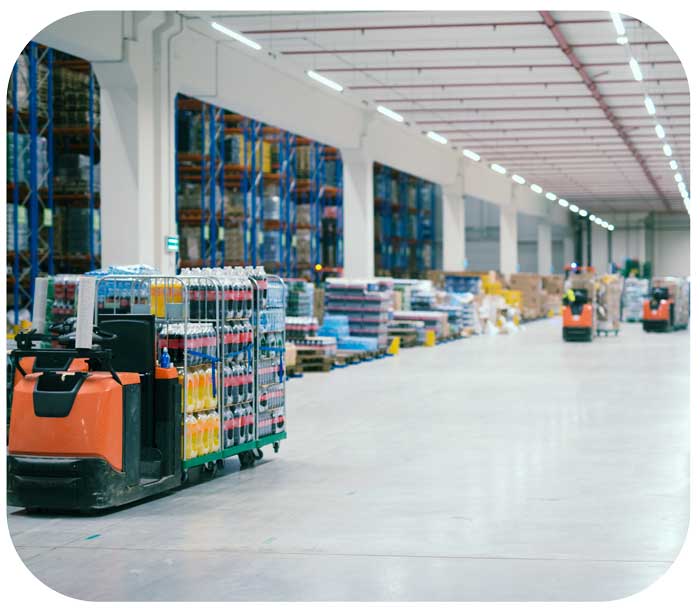
Optimized Equipment Usage
Managing equipment is a crucial step when optimizing production time. Ensuring each machine is working at its top efficiency, and being aware of when servicing equipment is necessary proves essential. For a worker to notice this could take a large amount of time.
Production monitoring provides the necessary solution to this issue. By noticing an error or possible improvement faster than that of a human inspector, maintenance could be scheduled as soon as the problem arises. Hence, it can save time and money by addressing the issue as soon as possible, and ensuring production is not disrupted longer than needed.
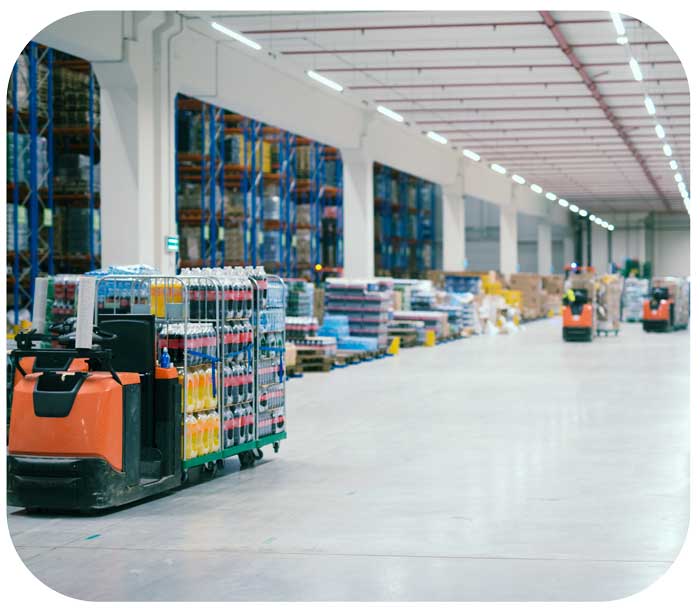
Optimized Equipment Usage
Managing equipment is a crucial step when optimizing production time. Ensuring each machine is working at its top efficiency, and being aware of when servicing equipment is necessary proves essential. For a worker to notice this could take a large amount of time.
Production monitoring provides the necessary solution to this issue. By noticing an error or possible improvement faster than that of a human inspector, maintenance could be scheduled as soon as the problem arises. Hence, it can save time and money by addressing the issue as soon as possible, and ensuring production is not disrupted longer than needed.
How Clariprod Can Help
Clariprod’s simple installation, interface, and accurate results provide manufacturers with the production line monitoring system they need. Clariprod allows you to automate all data collection from your machines and can centralize important data in one place. Using its real-time data acquisition, determining your overall equipment effectiveness and production errors is an easy task. Clariprod is also equipped with cellular alerts to inform employees in the case of production problems and allow for a quick fix. It is also a way to automate communication between employees, which saves time but also avoids errors. As a result, manufacturing costs and labor time will be reduced significantly, and therefore will allow for precious time and money to be used elsewhere. If you would like more information regarding Clariprod, don’t hesitate to contact us or visit our website: https://clariprod.com